新闻导航
冲压模具中氮气弹簧的合理应用窍门
【概要描述】
冲压模用氮气弹簧的优势分析,实例分析,具体工艺分析
详情
文章内容源自网络,本网站编辑后发布目的在于传递更多信息,版权归原作者所有。
概述
氮气弹簧顾名思义也是弹簧的一种。在汽车模具设计过程中,需要大量的弹性元件。如常规弹簧、聚氨酯、橡皮以及机床本身的气垫等。这些弹性元件在各个工业领域都被广泛应用,解决了各种弹性储能及冲压件卸料的问题。在汽车模具工业中,更是被大量使用。
这些年来,汽车模具工业技术和模具制造水平有了很大的发展和提高。汽车改型的加快,对模具的需求量也越来越大,模具朝着精密、复杂、高效及长寿命的方向迅速发展。
原有的常规弹性元件存在一定的缺点,不能满足这种形势的需要,不能理想地解决冲压工艺中的要求。这种情况往往会影响到冲压件的质量,使模具结构设计变得比较复杂,影响了模具在压力机上更换的时间。同时,常规弹性元件占有模具空间太大,有时为了解决冲裁力的问题,而增大模具外形尺寸,无形中增大了模具制造的成本。另外一个问题就是,弹性元件如果断裂,更换起来就比较费时费力,这样必然降低了模具的使用效率,降低了生产力。
冲压模用氮气弹簧的优势分析
模具用氮气弹簧是一种以高压氮气为工作介质的新型弹性组件。其工作过程可以近似的认为是等温膨胀和压缩过程。氮气弹簧的结构一般可分为活塞式和柱塞式两大类型,采用单腔或复腔的气室结构,气室设计上多为背压式结构。主要工作介质为高压氮气,密封在管路当中,不仅要很好地长期密封,并要在高压力下循环工作,这是一项综合性的技术。特点是体积小、弹力大、行程长、工作平稳,制造精密,使用寿命长(一百万次),弹力曲线平缓,以及不需要预紧等。并可以轻松地完成金属弹簧、橡胶和气垫等常规弹性组件难于完成的工作。简化模具设计和制造,方便模具安装和调整,延长模具的使用寿命,确保产品质量的稳定等。
实例分析
在模具设计中的应用,与大家共同探讨一下氮气弹簧在冲压模具中应用的优点。在某汽车公司车轮项目中,有一个直径为400mm的轮辐冲压件。在设计过程中,设计人员就遇到这样的难题。根据公式计算下来的冲裁力,需要普通重载弹簧30多根,可是受使用设备及模具外形尺寸的限制,没有足够的空间来布置如此多的弹簧。最终,尊龙凯时在此模具中采用氮气弹簧。使模具结构及外形尺寸大大简化。
在此模具设计中,选用了6根氮气弹簧。首先,从冲裁力的角度考虑,应先保证有足够的力量。其次,要考虑弹性元件在冲压过程中弹压力平衡传递的问题。从冲压工艺方面考虑,要提高冲压零件的质量一致性,提高模具使用寿命及减少模具其他零部件的磨损率,都必须考虑冲裁力的平衡问题。最后,力求使氮气弹簧压力系中心与冲压力中心重合。基于以上问题的考虑,最终选用6根氮气弹簧,均匀布置于压料芯之上,通过盖板固定于上模座。这样既减小了模具外形尺寸,又便于以后如果出现弹性元件失效后的维修。上模随机床滑块的运动不断进行相对运动,为了保证氮气弹簧工作的稳定性,钳工在装配时,必须保证氮气弹簧与盖板、盖板与上模座牢固并可靠连接。
加工装配完成后,在试模过程中,又出现了新的问题。由于氮气弹簧力量较大,使模具压料芯断裂。起初分析是否是压料芯材料的问题,后经材料分析排除了材料方面的原因。经工程人员及钳工的分析,决定在压料芯上加装橡胶来均匀力量,最终将此问题彻底解决。模具交付后,再没有出现此类问题。
具体工艺分析
在模具设计中的合理使用,也总结一些小的经验:落料工序,要求弹压力大、行程小。拉延工序一般要求行程比较大,在拉延过程中,弹压力基本保持恒定。这就要选择特性曲线比较平缓的氮气弹簧。对于顶出、卸件工序,要求有足够的力量和行程。在弯曲和翻边工序中,通常都要求初始力大,以便能压住工件,防止工件在弯曲和翻边过程中产生侧滑或移动,一般说来行程也要求比较大。不论在哪一种情况下选用,氮气弹簧的总高度不要太高,以避免发生不稳定的现象。如果将氮气弹簧安装在上模内,无论是顶件板还是压边芯,都必须留有间隙,以确保氮气弹簧平稳地工作。
结语
在选择氮气弹簧的过程中,行程和力量是最关键的。行程应满足冲压工艺的要求,不同的冲压工序,要求的行程大小是不一样的。目前,尊龙凯时在设计过程中,为了安全一般要求氮气弹簧的行程要比实际使用的行程大2~3mm。来保证氮气弹簧的安全性及使用寿命。当然,在模具设计中,各种弹性元件同时使用的例子也不在少数。只有充分合理的搭配使用,才能发挥各自特有的功效,共同提高模具使用寿命,更好地提高冲压件的质量
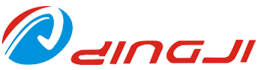
COPRYRIGHT © 2018 东莞市尊龙凯时精密模具有限公司 ALL RIGHT SERVERD